14 Process Engineer jobs in Vietnam
Process Engineer Intern
Posted 8 days ago
Job Viewed
Job Description
BINH DUONG PLANT
Job Description
P&G is a leading global consumer goods company whose winning brands are built around the model of innovation. Whatever your passion is, we want to ignite your potential to become your very best self. We hold true to our purpose, values and principles as we seek to make a difference in the world around us. You will engage in meaningful work that will touch the lives of others and have a real impact. Everything at P&G starts with understanding - understanding our consumers and our employees as we innovate to improve lives now and for generations to come.
What Success Looks Like
+ Understand end to end supply chain work process, identify top losses, develop, and execute the plan to eliminate the losses via digitalization.
+ Develop a seamless data flow and effective communication to organization via affordable solution complies to P&G and regulatory requirement (site scorecard, IWS content template & automation screen, etc.)
As an intern in Engineering:
+ Paid Learning Experience: We provide you with competitive stipend of monthly 12,000,000 VND
+ Responsibilities as of Day 1 - you will feel the ownership of your project from the beginning, and you will be given specific projects and responsibilities
+ Continuous coaching & mentoring- you will work with passionate people and receive both formal training as well as day-to-day mentoring from your manager and stakeholders.
+ Dynamic and respectful work environment - employees are at the core; we value every individual and encourage initiatives promoting agility and work/life balance
+ Full-time Opportunities: We love talented people; you will have the opportunity to become full-time following successful completion of your Internship.
You will be based in P&G Binh Duong Plant.
Job Qualifications
+ Third/final-year student that can work full-time from July 2025, with expected graduation in 2025, with STEM background (Electrical, Mechanical, Industrial, Chemical, Environmental, etc.)
+ English Fluency (written and spoken).
+ You are an excellent visionary, strategic and fearless leadership skills
+ You display strong teamwork, analytical skills, problem solving and solutions-oriented mindset especially during issues
+ You have an ability to drive innovation and business growth
+ You have ability to handle multiple priorities and take initiative and show flexibility
---
At P&G, we don't just offer a job, we provide a career with diverse assignments and numerous development opportunities to groom our future leaders!
About us
We produce globally recognized brands and we grow the best business leaders in the industry. With a portfolio of trusted brands as diverse as ours, it is paramount our leaders are able to lead with courage the vast array of brands, categories and functions. We serve consumers around the world with one of the strongest portfolios of trusted, quality, leadership brands, including Always®, Ariel®, Gillette®, Head & Shoulders®, Herbal Essences®, Oral-B®, Pampers®, Pantene®, Tampax® and more. Our community includes operations in approximately 70 countries worldwide.
Visit to know more.
Our consumers are diverse and our talents - internally - mirror this diversity to best serve it. That is why we're committed to building a winning culture based on Inclusion and our ideal candidate is passionate about the same principle: you will join our daily effort of being "in touch" so we craft brands and products to improve the lives of the world's consumers now and in the future. We want you to inspire us with your unrivaled ideas.
We are committed to providing equal opportunities in employment. We do not discriminate against individuals on the basis of race, color, gender, age, national origin, religion, sexual orientation, gender identity or expression, marital status, citizenship, disability, veteran status, HIV/AIDS status, or any other legally protected factor.
Job Schedule
Full time
Job Number
R000134574
Job Segmentation
Internships (Job Segmentation)
Manufacturing Process Engineer, Senior
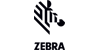
Posted 27 days ago
Job Viewed
Job Description
Overview:
At Zebra, we are a community of innovators who come together to create new ways of working to make everyday life better. United by curiosity and care, we develop dynamic solutions that anticipate our customer's and partner's needs and solve their challenges.
Being a part of Zebra Nation means being seen, heard, valued, and respected. Drawing from our diverse perspectives, we collaborate to deliver on our purpose. Here you are a part of a team pushing boundaries to redefine the work of tomorrow for organizations, their employees, and those they serve.
You have opportunities to learn and lead at a forward-thinking company, defining your path to a fulfilling career while channeling your skills toward causes that you care about - locally and globally. We've only begun reimaging the future - for our people, our customers, and the world.
Let's create tomorrow together.
This position is responsible for providing facilities and manufacturing support (continuous/process improvement and troubleshooting) in a regulated GMP environment.Design, develop, analyze, and implement manufacturing process in collaboration with Tier 1 suppliers or Distribution Centers. Lead Tier 1 suppliers or Distributions center teams to identify the root causes and resolution of manufacturing and quality issues. Drive day to day manufacturing operation and New Product Introduction. Supports various operational groups in cost reduction projects of Mass Production and New Products Introduction.Drive continuous improvement to enhance quality, efficiency and cost using LSS and I4.0 as framework
Responsibilities:
Support the implementation of Zebra's contract with electronic manufacturing services company ( EMS) by managing and monitoring the manufacturing activities carried out by the EMS and reporting to the global or regional team from time to time and performing duties in line with the company's overall strategy and direction for its product portfolio:
- Lead, implement and validate Lean Six Sigma and Industry 4.0 maturity level with Tier 1 suppliers or Distribution Centers.
- Drive process improvements using LSS and I4.0 tools: for example: Line Balancing, Continuous Flow Line Layout, Point of Use, 5S, TPM, OMS, Cross training, CTQ, PFMEA, Automation, Digitization solutions, etc.
- Conduct LSS & I4.0 audits to measure maturity level and identify opportunities and gaps.
- Work with internal and external teams to analyze and improve process focusing on root cause and eliminate the re-occurrence.
- Manage Engineering Change, Deviations and MFGO process: Evaluating the impact, risk, and material disposition.
- Review and approve work instructions and validate the approved manufacturing process and parameter are correctly implemented.
- Ensure production BOM is accurate and aligned with Agile references.
- Drive Cost reduction projects implementation with cross functional teams.
- Manage assets/fixtures/tools development/fabrication/validation/management.
- Review and update Labor and MVA Models.
- Makes and implements recommendations to improve process capabilities for Mass Production and New Products introduction.
- Develops positive relationships with other engineering disciplines and other functions for solving problems and innovative solutions implementation.
Qualifications:
- Minimum Education:
o BS degree in Engineering
- Minimum Work Experience (years):
o At least four (4) years of systems integration experience working with, designing, building and troubleshooting electromechanical systems, PLC's, data acquisition systems, electronic signals, process automation, etc.
- Key Skills and Competencies:
o Regulated (GMP) environments including Medical Devices, Personal Care, or Pharmaceutical manufacturing.
o Systems integration.
o Equipment/process qualification/validation.
o Preparing and training technicians/operators
o Printing and web handling.
o Working knowledge of LEAN and/or Six Sigma (E.g., Design of Experiments & Root-Cause Analysis).
o Creating cost models and performing feasibility analysis.
o Understanding of computers, networks and information systems.
o Working with cross-functional teams including Product Development, Analytical, Safety, Regulatory, Technology Assurance (or equivalent), and Quality Assurance (where applicable), in a technical role.
Position Specific Information:
- Travel Requirements - 5% of the time
- Personal Protective Equipment (PPE) Required (safety glasses, steel-toed boots, gloves, etc.): Steel-toed boots, safety glasses, others supplied by company.
U.S. Only - Frequency Definitions for Physical Activities, Environmental Conditions and Physical Demands:
Never - 0%
Occasionally - 0-20 times per shift or up to 33% of the time
Frequently - 20-100 times per shift or 33-66% of the time
Constantly - Over 100 times per shift or 66-100% of the time
Physical Activities (U.S. only):
Select the frequency for each item on the below list (never, occasionally, frequently, constantly).
- Ascending or descending ladders, stairs, scaffolding, ramps, poles and the like. (Occasionally)
- Working from heights such as roofs, ladders, or powered lifts. (Occasionally)
- Moving self in different positions to accomplish tasks in various environments including awkward or tight and confined spaces. (Occasionally)
- Remaining in a stationary position, often standing or sitting for prolonged periods. (Occasionally)
- Stooping, kneeling, bending, crouching, reaching, pushing/pulling. (Occasionally)
- Moving about to accomplish tasks or moving from one worksite to another. (Constantly)
- Adjusting or moving objects up to 20 pounds in all directions. (Occasionally)
- Communicating with others to exchange information. (Constantly)
- Repeating motions that may include the wrists, hands and/or fingers. (Never)
- Operating machinery and/or power tools. (Occasionally)
- Operating motor vehicles, industrial vehicles, or heavy equipment. (Never)
- Assessing the accuracy, neatness and thoroughness of the work assigned. (Occasionally)
Environmental Conditions (U.S. only):
Select the frequency for each item on the below list (never, occasionally, frequently, constantly).
- Exposure to extreme temperatures (high or low). (Occasionally)
- Outdoor elements such as precipitation and wind. (Occasionally)
- Noisy environments. (Occasionally)
- Other hazardous conditions such as vibration, uneven ground surfaces, or dust & fumes. (Occasionally)
- Small and/or enclosed spaces. (Never)
- No adverse environmental conditions expected. (Never)
Physical Demands (U.S. only): (Light work that includes moving objects up to 20 pounds.) Must be able to see color. (No)
Rewards Only Section:
FLSA Exemption (U.S. only):
For Exempt classifications only, what exemption was used when grading the job
1) Administrative
2) Computer
3) Professional
4) Executive
5) Outside Sales
6) Highly compensated
To protect candidates from falling victim to online fraudulent activity involving fake job postings and employment offers, please be aware our recruiters will always connect with you via @zebra.com ( email accounts. Applications are only accepted through our applicant tracking system and only accept personal identifying information through that system. Our Talent Acquisition team will not ask for you to provide personal identifying information via e-mail or outside of the system. If you are a victim of identity theft contact your local police department.
Principle Supplier Process Engineer (Mechanical)
Posted 6 days ago
Job Viewed
Job Description
Join us to do the best work of your career and make a profound social impact as a **Global Supplier Quality Engineer** on our **Mechanical** **Principle Supplier Process Engineering** Team in **Hanoi, Vietnam** .
**What you'll achieve**
As a Principle Supplier Quality Engineer, you will be responsible for the quality of Mechanical Chassis products used across all lines of business within Dell. You will manage multiple suppliers ensuring the adopt the latest automated manufacturing processes, monitoring their process and test yields. You will get the opportunity to work with various Dell electrical design teams and get involved with designs from an early stage through design for manufacturing reviews.
**You will:**
+ Be part of the cross functional Core Teams
+ Work directly with Supplier and Dell design teams.
+ Lead suppliers to drive for best in class manufacturing processes.
+ Work closely with other supplier quality engineers in Asia, US and Europe.
**Take the first step towards your dream career**
Every Dell Technologies team member brings something unique to the table. Here's what we are looking for with this role:
**Essential Requirements**
+ Excellent organizational, communication and problem solving skills. Strong interpersonal skills.
+ Minimum 7-10 years Mechanical quality experience with a Bachelor Degree.
+ Ability to rationalize strategic direction into meaningful actions.
+ Excellent English written and verbal communication skills.
+ In depth understanding of basic Engineering and power supply principles.
**Desirable Requirements**
+ Experience in conducting Audits of suppliers factories.
+ Use of standard quality tools, 8D's, 5C's, DFX etc.
**Who we are**
We believe that each of us has the power to make an impact. That's why we put our team members at the center of everything we do. If you're looking for an opportunity to grow your career with some of the best minds and most advanced tech in the industry, we're looking for you.
Dell Technologies is a unique family of businesses that helps individuals and organizations transform how they work, live and play. Join us to build a future that works for everyone because Progress Takes All of Us.
Dell Technologies is committed to the principle of equal employment opportunity for all employees and to providing employees with a work environment free of discrimination and harassment. Read the full Equal Employment Opportunity Policy here ( .
**Job ID:** R273485
Senior Principal Supplier Process Engineer
Posted today
Job Viewed
Job Description
What you’ll achieve:
As a member of the Supplier Quality Engineering, you will be responsible for new Tech development, supplier quality management to hit quality metrics and sustain Continuity of Supply (COS). This job requires strong process knowledge, rich practical experience, excellent communication, influencing skills and project management skills. Besides that:
What you’ll achieve
As a Principal Supplier Process Engineer, you will be responsible for supplier quality management to hit quality metrics and sustain Continuity of Supply.
You will:
- Enable new supplier, lead supplier process audit and qualification, drive supplier’s improvement actions on the findings and follow up closure. Supplier NPI management and phase gate review, solve NPI issue to ensure platform RTS on time.Supplier transfer of work review to meet company supplier chain strategy.
- Supplier process spot audit to drive supplier continuous improvement.Follow up commodity quality strategy deployment in supplier side, coach supplier in need.Contribute ideas to drive the innovative/optimize supplier manufactory process solutions for notebook commodities.
- Supplier quality KPIs performance monitor and supplier data analysis, drive supplier improvement opportunity.Improve supplier capability for quality plan/quality assurance/control.Drive supplier to solve quality issue via quality knowledge and logical thinking to mitigate schedule/delivery impact.
- Deploy Dell supplier management strategy in supplier side, monitor and review supplier execution.Work with cross function team together, provide and feedback supplier manufactory information.
- Support Device team’s projects.
**Take the first step towards your dream career**
Every Dell Technologies team member brings something unique to the table. Here’s what we are looking for with this role:
**Essential Requirements**
- Minimum 10 years relevant experience in related industry, proficient in manufacturing process knowledge, and IC industry experience is preferred with a Bachelor Degree in Engineering.
- Familiar with quality tools such as 6sigma, AQP, PFMEA, SPC, MSA, Fishbone, 5Why etc.
- Passion to solve problems, eager to learn new stuff, rigor on deliver quality result.
- Good communication skills in both English and Chinese
- Must be willing to travel to ODM sites at HaNam/ Bac Ninh at least 3 days a week.
**Desirable Requirements**
- Experience leading cross-functional teams to lead the decision-making process across multiple areas of the business.
- Ability to speak well in Chinese
**Who we are**
We believe that each of us has the power to make an impact. That’s why we put our team members at the center of everything we do. If you’re looking for an opportunity to grow your career with some of the best minds and most advanced tech in the industry, we’re looking for you.
Dell Technologies is a unique family of businesses that helps individuals and organizations transform how they work, live and play. Join us to build a future that works for everyone because Progress Takes All of Us.
Dell Technologies is committed to the principle of equal employment opportunity for all employees and to providing employees with a work environment free of discrimination and harassment.
**Job ID**:R241355
**Dell’s Flexible & Hybrid Work Culture**
At Dell Technologies, we believe our best work is done when flexibility is offered.
We know that freedom and flexibility are crucial to all our employees no matter where you are located and our flexible and hybrid work style allows team members to have the freedom to ideate, be innovative, and drive results their way. To learn more about our work culture, please visit our locations page.
Non-motor, Process Improvement Analyst
Posted today
Job Viewed
Job Description
(Mức lương: Thỏa thuận)
- Contribute to and take responsibility for the improvement/development of non-motor processes to minimize the involvement of the underwriting team on target risks for both RN and NB across AMCM.
- Help the company to drive non-motor sources more to standardize/align and automate the underwriting approaches (risk info, documentation, etc ) to reduce operational and underwriting risk.
- Initiate and lead the country teams to redesign the underwriting screens, tools, and processes to have a better user experience.
- Develop strong relationships with the stakeholders to inspire, align and lead them for the workflow changes to achieve a more process-oriented environment.
- Lead to roll out, monitor and follow the necessary actions for all non-motor process-related projects including ad-hoc projects.
- Build a non-motor process team to help the company to manage the transformation initiatives across Asia MCM.
- Involve and coordinate at least monthly meetings to update stakeholders about the ongoing/future projects and KPIs across Asia MCM.
**Chức vụ**: Nhân Viên/Chuyên Viên
**Hình thức làm việc**: Toàn thời gian
**Quyền lợi được hưởng**:
Thưởng trên hiệu quả công việc
Bảo hiểm Sức khỏe/Bảo Hiểm Tai Nạn
Nghỉ phép có lương/Làm việc linh động
**Yêu cầu bằng cấp (tối thiểu)**: Đại Học
**Yêu cầu công việc**:
- Bachelor in business, analytics, economics, or a similar field required.
- 5-8+ years of process improvement experience in retail non-life insurance products mainly non-Motor.
- Proven track record of process development/improvement.
- Exhibit business acumen and strategic thinking.
- Ability to communicate and askquestions that relate to the work.
- Advance knowledge ofadvanced in-office programs.
**Yêu cầu giới tính**: Nam/Nữ
**Ngành nghề**: Hành Chính/Văn Phòng,Quản Lý Chất Lượng (QA/QC)
Đại Học
5 - 8 năm
Staff for Process Improvement [ Q.1 - Hcm ]
Posted today
Job Viewed
Job Description
- The mission of this position is to maintain the basic quality required by CAINZ and to improve the quality control and factory process control standards at client factories, leading to the shipment of all good products.
- Travel to client factories, mainly in Vietnam but also in neighboring countries such as Cambodia and Thailand, to identify problem areas and provide guidance for process improvement at the work site.
- PDCA follow-up (organizing and managing meetings) to determine the causes of the above problems and implement countermeasures.
- Provide advice and guidance to improve the management level of the factory, not only for on-site improvement.
- Analyze and implement preventive measures by process FMEA and FTA for quality problems at suppliers.
- Participate in the production witness at the time of mass production to prevent the occurrence and outflow of quality problems. Confirm that improvement points are being implemented as planned.
- Conduct process audits to point out problems and seek improvements.
- When quality problems occur, confirm local process issues (grasp current status), analyze causes, plan countermeasures, confirm implementation, and lead progress according to QC story.
- Cooperate with superiors (Japanese).
- Assist in general operations of the Vietnam office in cooperation with the supervisor and the sales side.
**Job requirements**:
- Japanese N2 level or above.
- Bright personality.
- Good communication skills.
- Able to go on overseas business trips by yourself (from Vietnam to neighboring Asian countries).
- About once a month for business trip with overnight stay, about 5 times a year for overseas business trip.
- Experience in the following areas at a manufacturer is desirable.
- Production engineering, manufacturing engineering, quality assurance, quality control, etc.
- English is plus.
- **Bonus**:
- Bonus once a year.
- Salary increase once a year.
- Meal allowance.
- Transportation allowance.
- Lodging allowance(240,000 VND per night, with allowances depending on position).
**Job workplaces**:
- Hồ Chí Minh - Việt Nam
**Job level**:
- Nhân viên
**Job language**:
- Tiếng Nhật
**Job industry**:
- Thiết kế quy trình & Sản xuất
Process Equip Engineer for Dw
Posted today
Job Viewed
Job Description
At Intel, we are always learning new things and pushing the boundaries.and that drives amazing experiences. We want you to dream big and help us take on some of the biggest technical challenges in the industry.
Intel Vietnam is the largest factory in Intel's global Assembly and Test network and a critical site for our IDM2.0 strategy. The Assembly Engineering department (AE) is an important part of this vision, in charge of assembling our silicon into microprocessors.
We are looking welcome a Module Engineer into our team. A highly energetic individual with strong technical background to drive engineering solutions and enable new technology transfers.
Join us in our journey to create world-changing technology that improves the life of every person on the planet.
**Responsibilities**:
- Empowered to lead critical resolution of operational needs for the Assembly process and equipment.
- Optimize advance process control systems to detect signals and automate containment.
- Define maintenance procedures, engage and partner with technicians and manufacturing teams to maintain equipment meeting highest standards.
- Discover and enable new breakthroughs process and equipment improvements.
- Engage and lead new technology/product transfers and integration.
- Actively engaged in our Virtual Factory (VF) network, driving cross site learnings and problem resolution
**Qualifications**:
- Possess a Bachelor or a Master of Science degree in Electrical, Mechanical, Mechatronics, Chemical and/or other related majors.
- Strong English verbal and written communication skills.
- Self-motivated, team-oriented individual with a strong data driven mindset and positive learning attitude.
- Familiarity with semiconductor packaging and technologies would be an added advantage.
- At least 2 years of relevant working experience.
**Inside this Business Group**:
As the world's largest chip manufacturer, Intel strives to make every facet of semiconductor manufacturing state-of-the-art - from semiconductor process development and manufacturing, through yield improvement to packaging, final test and optimization, and world class Supply Chain and facilities support. Employees in the Technology Development and Manufacturing Group are part of a worldwide network of design, development, manufacturing, and assembly/test facilities, all focused on utilizing the power of Moore’s Law to bring smart, connected devices to every person on Earth.
**Posting Statement**:
All qualified applicants will receive consideration for employment without regard to race, color, religion, religious creed, sex, national origin, ancestry, age, physical or mental disability, medical condition, genetic information, military and veteran status, marital status, pregnancy, gender, gender expression, gender identity, sexual orientation, or any other characteristic protected by local law, regulation, or ordinance.
**Benefits**:
We offer a total compensation package that ranks among the best in the industry. It consists of competitive pay, stock, bonuses, as well as, benefit programs which include health, retirement, and vacation. Find more information about all of our Amazing Benefits here.
**Working Model**:
This role will require an on-site presence.
JobType
On-site Required
Be The First To Know
About the latest Process engineer Jobs in Vietnam !
Process Equip Engineer for Cam
Posted today
Job Viewed
Job Description
At Intel, we are always learning new things and pushing the boundaries.and that drives amazing experiences. We want you to dream big and help us take on some of the biggest technical challenges in the industry.
Intel Vietnam is the largest factory in Intel's global Assembly and Test network and a critical site for our IDM2.0 strategy. The Assembly Engineering department (AE) is an important part of this vision, in charge of assembling our silicon into microprocessors.
We are looking welcome a Module Engineer into our team. A highly energetic individual with strong technical background to drive engineering solutions and enable new technology transfers.
Join us in our journey to create world-changing technology that improves the life of every person on the planet.
**Responsibilities**:
- Empowered to lead critical resolution of operational needs for the Assembly process and equipment.
- Optimize advance process control systems to detect signals and automate containment.
- Define maintenance procedures, engage and partner with technicians and manufacturing teams to maintain equipment meeting highest standards.
- Discover and enable new breakthroughs process and equipment improvements.
- Engage and lead new technology/product transfers and integration.
- Actively engaged in our Virtual Factory (VF) network, driving cross site learnings and problem resolution.
**Qualifications**:
- Possess a Bachelor or a Master of Science degree in Electrical, Mechanical, Mechatronics, Chemical and/or other related majors.
- Strong English verbal and written communication skills.
- Self-motivated, team-oriented individual with a strong data driven mindset and positive learning attitude.
- Familiarity with semiconductor packaging and technologies would be an added advantage.
- At least 2 years of relevant working experience.
**Inside this Business Group**:
As the world's largest chip manufacturer, Intel strives to make every facet of semiconductor manufacturing state-of-the-art - from semiconductor process development and manufacturing, through yield improvement to packaging, final test and optimization, and world class Supply Chain and facilities support. Employees in the Technology Development and Manufacturing Group are part of a worldwide network of design, development, manufacturing, and assembly/test facilities, all focused on utilizing the power of Moore’s Law to bring smart, connected devices to every person on Earth.
**Posting Statement**:
All qualified applicants will receive consideration for employment without regard to race, color, religion, religious creed, sex, national origin, ancestry, age, physical or mental disability, medical condition, genetic information, military and veteran status, marital status, pregnancy, gender, gender expression, gender identity, sexual orientation, or any other characteristic protected by local law, regulation, or ordinance.
**Benefits**:
We offer a total compensation package that ranks among the best in the industry. It consists of competitive pay, stock, bonuses, as well as, benefit programs which include health, retirement, and vacation. Find more information about all of our Amazing Benefits here.
**Working Model**:
This role will require an on-site presence.
JobType
On-site Required
Tooling Repair Base (Trb) Process Equip Engineer
Posted today
Job Viewed
Job Description
**Qualifications**:
- Pursuing a degree in Electronic/Electrical Engineering, Automation Control, Computer Engineering, or a related field.
- Computer literacy and basic math skills are required.
- Possess statistical data analysis and data system automation skills.
- Good verbal/written communication skills with the ability to effectively communicate with peers, and customers.
- Capable of handling multi-task and support other team members
- Able to work both independently and in a team-oriented environment.
Preferred Qualifications:
- Familiarly with analytics tool such as PowerBI/Tableau, etc
- Intermedia proficiency in any language and scripting such as Python, C#/C++,etc
**Inside this Business Group**:
As the world's largest chip manufacturer, Intel strives to make every facet of semiconductor manufacturing state-of-the-art - from semiconductor process development and manufacturing, through yield improvement to packaging, final test and optimization, and world class Supply Chain and facilities support. Employees in the Technology Development and Manufacturing Group are part of a worldwide network of design, development, manufacturing, and assembly/test facilities, all focused on utilizing the power of Moore’s Law to bring smart, connected devices to every person on Earth.
**Posting Statement**:
All qualified applicants will receive consideration for employment without regard to race, color, religion, religious creed, sex, national origin, ancestry, age, physical or mental disability, medical condition, genetic information, military and veteran status, marital status, pregnancy, gender, gender expression, gender identity, sexual orientation, or any other characteristic protected by local law, regulation, or ordinance.
**Benefits**:
**Working Model**:
This role will require an on-site presence.
Process and Equipment Engineer (Assembly
Posted today
Job Viewed
Job Description
At Intel, we are always learning, and with that learning comes amazing experiences. We want you to dream big and help us take on some of the biggest technical challenges in the industry.
Intel Products Vietnam is the largest manufacturing facility in Intel's global Assembly and Test network. The Assembly Engineering department (AE) is an engineering powerhouse comprising of highly motivated, data driven and result oriented individuals diverse in ideas and experience. We are looking welcome a Process and Equipment Engineer into our team. A highly energetic individual with strong technical background to drive engineering solutions and enable new technology transfers.
Join us in our journey to create world-changing technology that improves the life of every person on the planet.
**Responsibilities**:
- Empowered to lead critical resolution of operational needs for the Assembly process and equipment.
- Optimize advance process control systems to detect signals and automate containment
- Define maintenance procedures, engage and partner with technicians and manufacturing teams to maintain equipment meeting highest standards.
- Discover and enable new breakthroughs process and equipment improvements.
- Engage and lead new technology product transfers and integration.
**Qualifications**:
- Possess a Bachelor or a Master of Science degree in Electrical, Mechanical, Mechatronics and or other related majors.
- Strong verbal and written communication skills in English.
- Self-motivated, team oriented, data driven mindset and positive learning attitude.
- Able to work on 12 hours shift (based on business need with additional allowances).
- Familiarity with semiconductor packaging and technologies would be an added advantage.
- 0-2 years of experience.
**Inside this Business Group**:
As the world's largest chip manufacturer, Intel strives to make every facet of semiconductor manufacturing state-of-the-art - from semiconductor process development and manufacturing, through yield improvement to packaging, final test and optimization, and world class Supply Chain and facilities support. Employees in the Technology Development and Manufacturing Group are part of a worldwide network of design, development, manufacturing, and assembly/test facilities, all focused on utilizing the power of Moore’s Law to bring smart, connected devices to every person on Earth.
**Posting Statement**:
All qualified applicants will receive consideration for employment without regard to race, color, religion, religious creed, sex, national origin, ancestry, age, physical or mental disability, medical condition, genetic information, military and veteran status, marital status, pregnancy, gender, gender expression, gender identity, sexual orientation, or any other characteristic protected by local law, regulation, or ordinance.
**Benefits**:
**Working Model**:
This role will require an on-site presence.
JobType
On-site Required